An Eye-Opening Guide to Pressure sensor Types: Everything You Need to Know
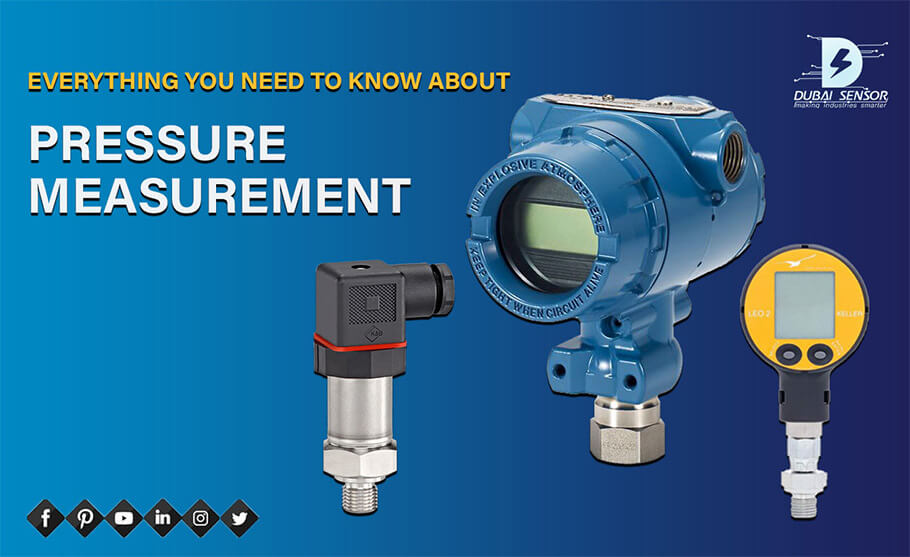
Pressure is the second most measured parameter in the industry. It is the fundamental parameter required to measure some other industrial parameters. For instance, by pressure measurement, you can measure density, flow, etc.
Still wondering what the first most measured parameter is? Well, It is temperature. Now, May I have your concentration on the pressure again, please?
This article reveals almost any concept related to pressure measuring and different pressure sensor types. And It will guide you to other articles to read more about them. So let’s dive in.
What exactly does pressure mean?
The definition of pressure in physics is the perpendicular force per unit area. When reading this definition, the image of a solid item exerting force on a surface comes to mind. But as this image is totally correct, it is not the only image. Liquids and gases can exert pressure, too. As a matter of fact, we are constantly under the pressure of the earth's atmosphere, and that is not a small amount of pressure. So why don't we feel it? It is because the pressure is always there, and our body is designed to exert a reverse force to balance the air pressure. We can feel the change of the atmospheric pressure on the peak of a high mountain, though. So it would be a really awkward situation if you had been thrown into the vacuum outside the earth's atmosphere. Don’t worry! Your bones and skin are strong enough to protect you from exploding. But lack of oxygen and direct sun rays would harm you. Besides, As the pressure goes down, your saliva will reach its boiling point. Let us not continue with the things that would happen, just promise not to go to space without a spacesuit.
Okay, Let’s go back to our fascinating topic, pressure. As I was saying, gases and liquids exert pressure as well. Just like the atmospheric pressure, a column of liquid exerts pressure. Imagine yourself diving into a pool. The water column above you would exert a specific amount of pressure on you. Of course, it won’t be just the column of water, but that plus the atmospheric pressure. Keep in mind that this example was about the time the water was at rest. There is lots of difference when you dive into a water stream. That is when static, dynamic, and stagnation pressure come in. To know more about them, and also to get familiar with the pressure units, I invite you to check the below article:
Pressure [Explanation, Pressure Units, Types of Pressure (Static, Dynamic, Stagnation)]
Let's watch a video on what exactly a pressure sensor is
The difference you should know between absolute and gauge pressure
There are two main types of pressure measurement. They are known as absolute and gauge pressure. The difference? Well, it’s all about their reference point. Absolute pressure is the pressure measured related to the total vacuum, while gauge pressure is measured related to the atmospheric pressure at the sea level. Since atmospheric pressure depends on altitude, sea level is considered as a standard. One more thing about them, people also know gauge pressure as relative pressure.
I’m sure you’ve got there is a relation between absolute and gauge pressure. Let’s say that atmospheric pressure is determined by Pamb, then the relation would be:
Pg = Pabs - Pamb
As you can see, gauge pressure doesn’t depend on atmospheric pressure, while absolute pressure does. So when measuring absolute pressure, the result can be different based on your location. But there is no such issue in gauge pressure measurement. Even though when you use a sealed gauge pressure sensor, this kind of issue might happen. We discuss that problem in the following sections.
Measuring gauge pressure is more common, though. Why? Because atmospheric pressure is almost always there, and involving it in your calculations every time might seem pointless. Sometimes you need to know the absolute pressure though, which is always positive.
On the other hand, gauge pressure can be negative, zero, and positive:
• Negative: The pressure is less than atmospheric pressure
• Zero: The pressure exactly equals atmospheric pressure
• Positive: The pressure is higher than the atmospheric pressure
You may be thinking about differential pressure. Well, I have to say that it’s a specific type of relative pressure. Just like gauge pressure, differential pressure is the pressure measured related to another pressure value. This reference value is not necessarily the atmospheric pressure, though.
I think It’s good to know that absolute vacuum equals -101.325 mbar.
There are lots of fascinating facts about absolute, gauge, and differential pressure. If you’re interested to know more about them, feel free to step into the below article:
Types of Pressure (Absolute Pressure, Gauge Pressure, Differential Pressure)
Pressure measuring instruments you need to know
We learned a bit about pressure and the difference between absolute and gauge pressure, right? Now, it's time to dive into pressure-measuring instruments. You may call all these instruments pressure sensors. It is not wrong, quite frankly. But you have to keep in mind that there are four main types of pressure sensors. Cause, believe me, this way when choosing a pressure measuring instrument, the salesman won’t seem all greek to you. These four main types are:
• Pressure transducer
• Pressure transmitter
• Pressure switch
• Pressure gauge
Let’s get more specific. What is the main difference between these four? They all receive mechanical pressure on their process connection, but the main difference is in the output they provide.
The pressure transmitter and pressure transducer act almost the same. These two convert the inlet pressure to a millivolt signal in the first step. What makes a pressure transducer different from a pressure transmitter is its final output. A pressure transducer amplifies the millivolt signal to a voltage output signal. The most common voltage outputs are 0-5 V, 0-10 V, and 0.5-4.5 mV/V. On the other hand, the pressure transmitter converts the millivolt signal to a current output signal: mainly 4-20 mA.
A pressure switch, as its name represents, provides a switching output. Oh! Let me correct myself. It’s not always just one switching output. Some pressure switches can combine several switching outputs. Two main types of switching outputs are Normally Open (NO) and Normally Closed (NC). You can notice the difference between them, I bet. A Normally Open switch is open in the first place. As the pressure reaches the setpoint, the switch will act and the stream will be cut off. The Normally Closed switch acts vice versa. By pressure reaching the setpoint, the stream will start to flow.
A Pressure gauge though doesn’t outlet a signal. This instrument carries the responsibility for displaying the pressure on the field. There are two main pressure gauge types: Analog pressure gauge and digital pressure gauge.
There is one last point I like to mention here about these instruments. There can be some instruments that are a mixture of these devices. You may have a pressure gauge that also outputs a current signal, or you may have a pressure transmitter that provides a switching output as well. We gather more specifications about them in another blog post. Want to know more about them? Here you are:
Introducing any pressure sensor use you might need
There are so many aspects related to a pressure sensor, and we try to cover them here. But no, it’s time to mention pressure sensor uses, I think.
In today’s world, a pressure sensor is needed in almost all industries. But it’s not just the industry. Anywhere you need to know a media’s pressure and convert it to a kind of signal you have to use a pressure sensor. Let me be more specific. Different pressure sensor types are used in various fields, from a high-risk environment on earth such as the oil and gas industry, to up in the sky in an airplane, to even underwater in scuba diving instruments. Yes, you may need to measure pressure anywhere a human being can step.
In fact, remember me advising you not to go to space without a spacesuit? Well! Now I have another piece of advice for you: if you’ve found a spacesuit, carry some pressure sensors with you to the international space station. Let me give you a hint: make sure they have compound measuring ranges.
Reading this, lots of questions may come to your mind. You may like to know if a pressure sensor is an answer for your application. We gather almost any pressure sensor usage in another post. I invite you to visit there and read more about pressure sensor applications:
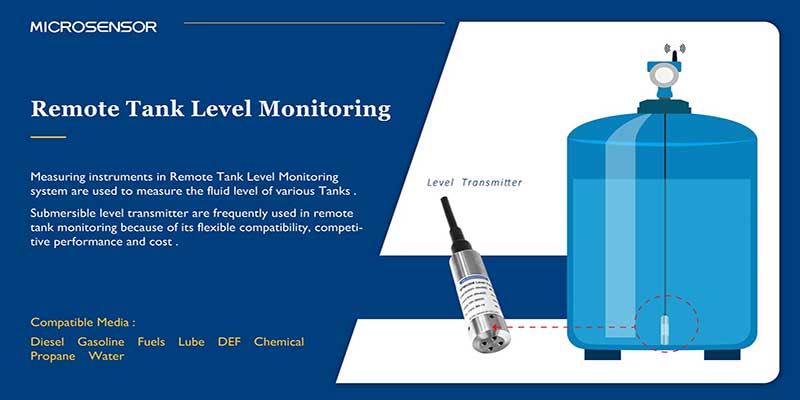
Remote Monitoring of the Fluid Level of Tanks
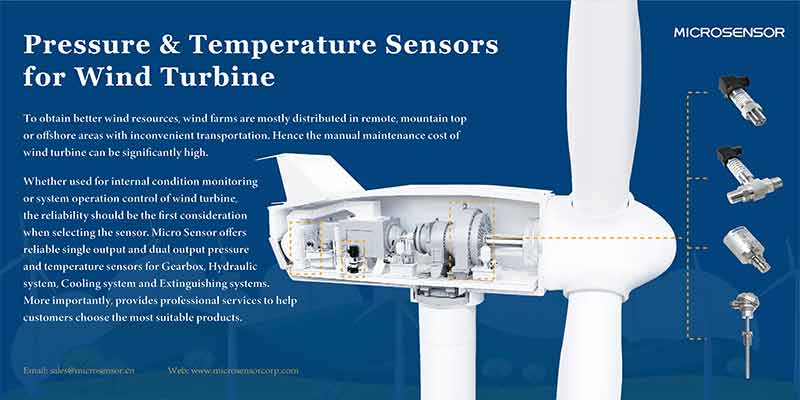
Temperature and Pressure Sensors Used for Wind Turbines
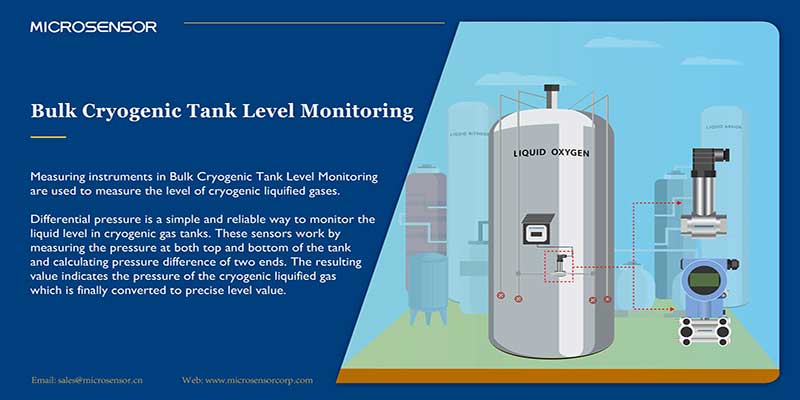
Monitoring the Level of Bulk Cryogenic Tanks
Everything about Pressure range in pressure sensors
The pressure Range is the maximum or the lowest to the highest value of pressure that a pressure sensor can measure accurately.
For example, if you have a pressure sensor with a 1000 psi maximum range, it cannot read the pressure values beyond 1000 psi.
Therefore, as a general rule, it is better to choose a pressure sensor that gives 40% to 50% more than the maximum rated pressure. Its benefit is that the sensor will perform better because it doesn’t get pushed to its limits all the time.
Vacuum and Compound pressure are 2 types of pressure range. If you want to know more, check out our Pressure Range Explanation in Pressure Sensors article now!
Pressure sensor measuring principles and technologies
Pressure sensing devices detect the changes in the pressure in gasses or liquids and convert them with high accuracy to an electrical output signal that is proportional to the pressure. This electrical output signal is used to represent the magnitude of the pressure. Electronic pressure sensors use several different technologies or sensing principles capable of converting pressure into a measurable and standardized electrical signal. The pressure sensor technology used in a pressure sensor can be important based on the application. Pressure sensors are made with different technologies, some of them that are explained in this article are;
• Thin-film sensors
• Thick-film sensors
• Piezoresistive sensors
Tap here to get more information about Measuring Principle of Pressure Sensors
Accuracy of Pressure Transmitters
According to the International Electro Technical Commission (IEC), the accuracy of a pressure sensor indicates the maximum positive or negative deviation from the ideal characteristic curve obtained by testing a device under certain conditions and processes. In other words, it represents the maximum difference between the actual value and the value reported (measured) by the device.
The accuracy of the pressure sensor is one of the most important factors in choosing a pressure sensor. There is no clear definition for accuracy and each manufacturer defines it with different variables influencing it.
Accuracy can be divided into several components, which are explained in our Accuracy of Pressure Transmitters article. Check it out!
Resolution, Sampling rate, Response Time of Pressure Sensors
The analogue - digital resolution of a pressure transmitter can be expressed as the smallest change of the analogue – digital – analogue conversion that can be measured by the signal processing of a pressure transmitter.
This is an important factor for determining the precision of a pressure transmitter in detecting a pressure variation.
The resolution of a pressure transmitter is expressed in percentage of FSO (Full Scale Output). To learn more about please refer to Resolution, Sampling rate, Response Time of Pressure Sensors article.
All Temperature Types Regarding Pressure Transmitter
When choosing a pressure sensor, the common concern is the performance of the sensor in various temperature conditions and the temperature range that is greater than the suitable minimum and maximum temperatures.
There are significant errors in the pressure measurement or complete failure of the sensor if it is installed in an environment that is exceeding the specified temperature ranges. To learn more about please refer to All Temperature Types Regarding Pressure Transmitter article.
Melt Pressure Transmitter and High-Temperature Transmitter
A Melt pressure sensor is used to detect and control the amount of temperature and pressure in plastic extrusion machines.
It is necessary to use the melt pressure sensor in the extruder to increase the quality of products, reduce waste, reduce the consumption of products to the machine and also improve the safety of the production line.
The melt pressure transmitter converts the physical pressure parameter into an electrical signal. Most melt pressure sensors use a kind of heat and pressure-resistant diaphragm to measure the amount of pressure.
The whole structure of this sensor is constructed such that it transmits the pressure applied by the medium, on the contact diaphragm to the transduction part, and keeps it away from the heat source. To learn more about Melt Pressure Transmitter and High-Temperature Transmitter please refer to our article.
Ingress Protection Vs. NEMA Enclosure Ratings in pressure sensors
IP or Ingress Protection is defined as an accepted standard in the IS (International Standard) EN 60529 to determine the resistance of electronic devices to the amount of the elements, as well as dust or moisture ingress.
In fact, IP rankings are important indicators to show us how much the body and outer cover of the equipment prevent the penetration of dust and water, in electrical enclosures. To learn more about Ingress Protection Vs. NEMA Enclosure Ratings please refer to our article.
Wetted Parts in Pressure Sensors (Diaphragm Seal, Capillary and Seal or O-ring)
Wetted parts are an important aspect to reflect on when choosing a pressure sensor. Process connections and wetted parts are the frontline dealing with the medium of application.
“Wetted parts” are measurement components used in connection with pressure sensors for all those parts, surfaces, and/or parts and also any internal seals, welds, or membranes/ diaphragms of the pressure sensors that are (potentially) exposed to or in direct contact with the media under pressure. To learn more about please refer to Wetted Parts in Pressure Sensors (Diaphragm Seal, Capillary and Seal or O-ring) article.
Process Connection or Fitting for Pressure Transmitter
When choosing a pressure sensor, you should notice the available process connection types. Process connections are used to install measurement instrumentation. There are many different process connection types all across the world, in this article the concentration will be on discussing the most common fittings and connection methods used to install valves and other process components in the piping of process systems.
They all perform the same function but each connection type has its own pros and cons. Choosing the best process connection type is based on the needs of each industry and according to international standards. Tap here to get more information about Process Connection or Fitting for Pressure Transmitter.
Certificates and Approvals Related to Pressure Transmitters
Pressure sensors have different approvals and certifications in terms of environmental, regional, and various applications. For example, some certificates like CE are used for trade in a specific region such as Europe, others such as ATEX for the use of sensors in hazardous and explosive areas, EHEDG for hygienic applications, and some are utilized in marine and shipbuilding industries. To know more, you can check Certificates and Approvals Related to Pressure Transmitters article.
Special Types of Pressure Sensors
In all industries there are applications which require special care and needs. For pressure measurement applications sometimes these needs are measuring a very hot medium, or a very strong wave of water. Here we want to explain some special types of pressure sensors which are equipped and enhanced to work in such situations. To learn more about please refer to Special Types of Pressure Sensors article.
Choose your pressure sensor from these 12 popular brands
Now you know the basics in any aspect related to a pressure sensor. But if you want to buy pressure sensors, you should get familiar with the pressure sensor brands and their series. There are 12 popular pressure sensor brands in UAE, and I’m sure you’ll find the answer to your needs among them. I’d like you to know that none of these brands is better than the others. It’s just about the application you want to use the pressure transmitter in.
Here is the list of the 12 most wanted pressure transmitter brands in UAE: Endress Hauser, WIKA, Rosemount, ABB, YOKOGAWA, Siemens, Setra, Omega, Honeywell, Keller, Hogller, and Microsensor.
In another post, we gathered the most popular series of these brands in Dubai. Are you excited to know them? Simply click on the link below:
Top 12 Popular Pressure Sensor Brands and Their Best Seller Products in UAE