Inductive Proximity Sensor Types [Working Principle, All Types Explained, Terminology, Outputs]

There are different methods of sensing that can be used to detect a target. We can determine a suitable method for a specific application based on different considerations: such as the environment of the application, type, and distance of object placed in front of the sensor.
Inductive sensors are designed specifically for the detection of conductive and any metal objects and also objects that can be detected from close proximity. Inductive sensor is used to detect multiple types of metal.
These sensors are non-contacting and performed based on induction law. When a metallic object comes close to the sensor, the oscillator coil starts to move.
When the object approaches within the detection range, the sensor uses an electromagnetic field that is sent out for detection of the object, then the sensor searches for changes in the returning signal. After detecting the object, the returning signal becomes shorter than when there is no object.
Let’s see how does a proximity sensor work?
There are unshielded and shielded versions of these sensors:
In the unshielded sensors, the Electromagnetic field generated by the coil is not restricted and has longer and larger sensing ranges.
The surface of the detection coil on shielded Proximity Sensors is covered with metal, so the electromagnetic field is concentrated at the front of Sensors.
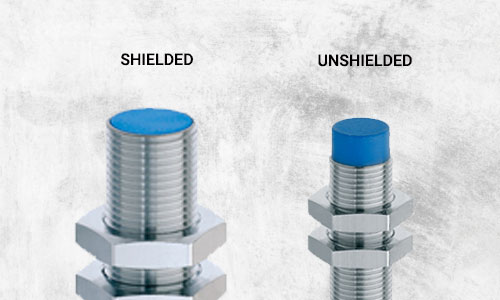
4 main components that make up the sensor are:
• Coil
• Oscillator
• Schmitt Trigger
• Output switching circuit
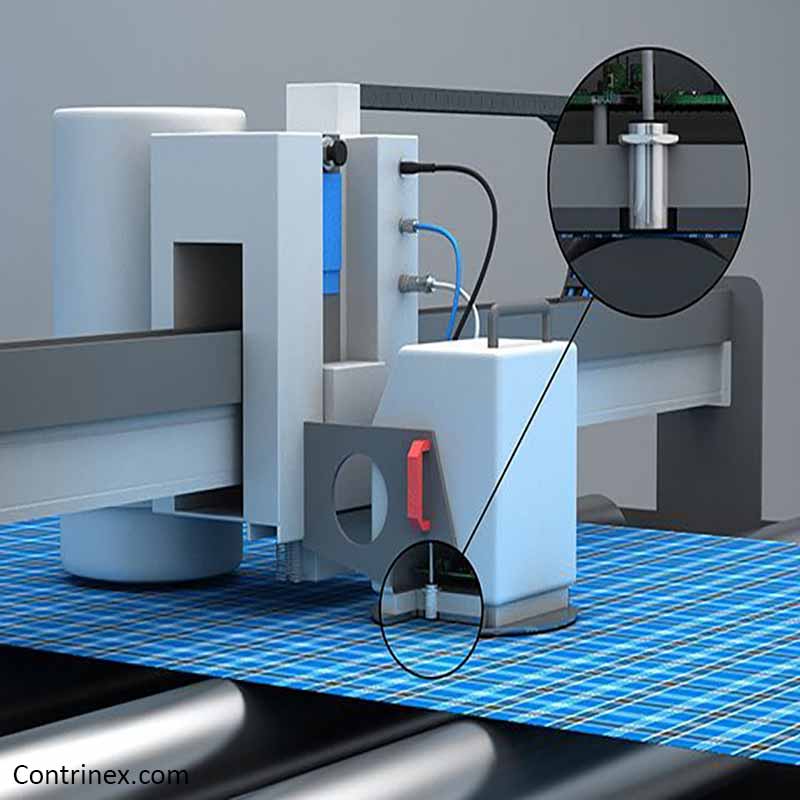
Stoutness of moving textile webs can be calculated by High-Resolution Analog Inductive Sensors.
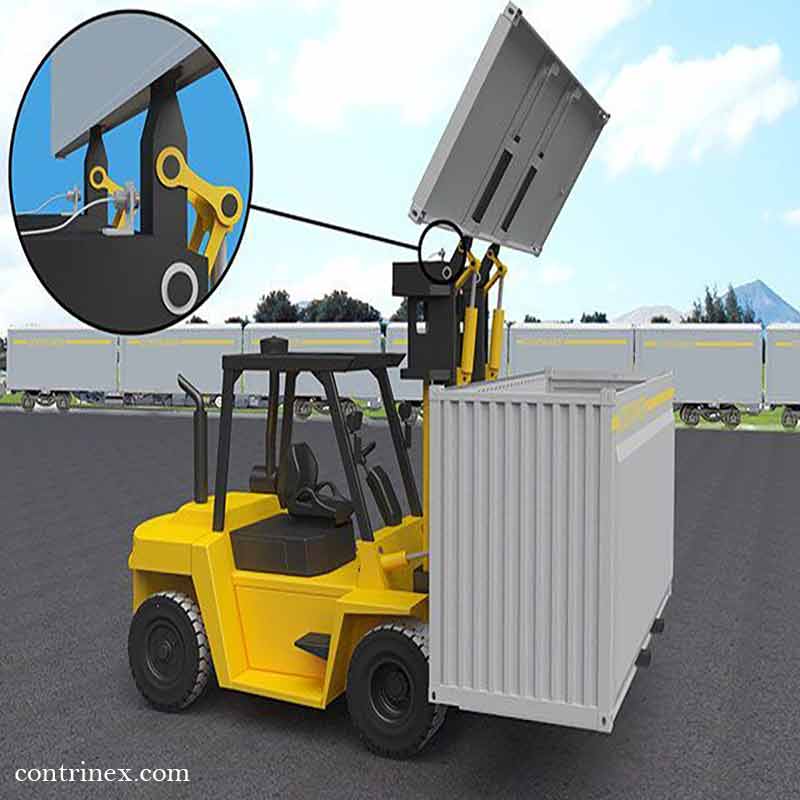
Inductive sensor detects the opening container.
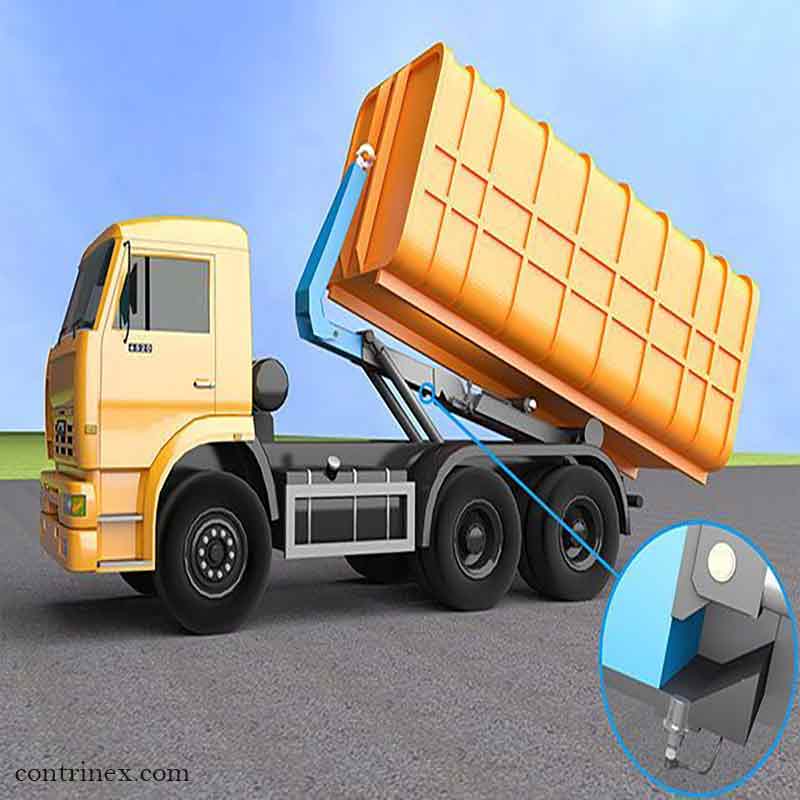
Inductive sensors help preventing overloading of hook lift truck arm.
Inductive sensor types
Inductive proximity sensors are categorized in 8 categories based on application:
Inductive Sensor
These sensors are used for non-contact object detection and nearby metallic objects. they are varies depending on the size and distance of the sensing object, body size, wiring type, etc.
Proximity sensors are available in various designs suited for different purposes and diffrent applications like beverage container packaging, automatic drilling machines, and shoe rubber press machines, forklift, door, truck, car, parking, mobile and cylindrical designs are a typical type of them.
They are used in different applications and industries such as transportation, robots, assembly lines, telecommunication, or security.
They have high precision and low sensitivity to environmental conditions and also can be used in harsh working conditions like with high temperature, high humidity. The biggest advantage of standard inductive sensors in industrial applications is the immunity against oil, water, and dirt.
The typical measuring range of inductive proximity sensors is between 0.1 cm and 5 cm. This article presents the working principle and types of standard inductive sensors that give you more sight to choose a suitable sensor for your business.
They come in diffrent body size, the important aspect in the body is the diameter of the sensor which comes in 8mm, 12mm, 18 mm and 30 mm.
High Pressure Proximity Sensor
Pressure Resistant proximity switches are a type of sensor that use in situations where there is high pressure and can withstand pressures.
In the manufacturing of High Pressure Proximity sensor, rugged stainless steel is used and the housing is extremely resistant against pressure and is full metal.
This sensor can be found in special demanding applications.
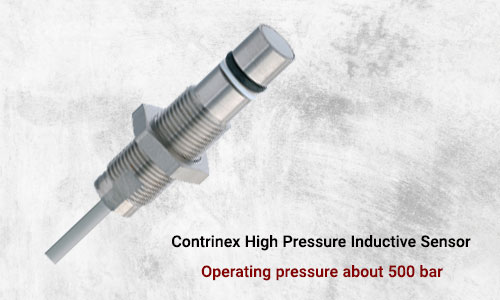
High Temperature Proximity Sensor
High Temp Proximity sensors are specialized for applications that extremely high temperatures are involved in the application.
Industrial furnaces, combustion chambers, metallurgical processing apparatuses, and glass industries are temperature-dependent systems that require constant thermal monitoring to maintain optimal working conditions.
These sensors are designed for use in situations the temperature is rated up to 180 ºC.
Some of the more common techniques used to reach this rating are:
• Special mechanical construction
• Select electronic components
• Replacing the standard housing material, PTB, with temperature-resistant material
To learn more about High Temperature Inductive Proximity Sensor please refer to our article.
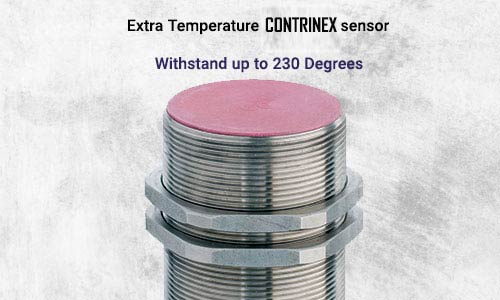
Rectangular Proximity Sensor
Rectangular Housing are space-saving flat housing sensors used in applications there are space limitations, and can not use standard cylindrical because there is not enough space.
There are two types of rectangular sensor in one type sensing face is placed on the small sides so the height of the sensor must be considered and in the other type sensing face is placed on the larger sides so the length of the sensor should be taken into account.
To learn more about Rectangular Inductive Proximity Sensor please refer to our article.
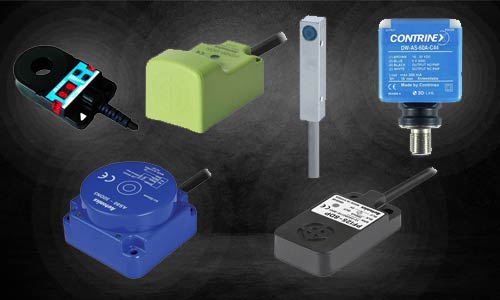
Analog Proximity Sensor
Analog Output Proximity sensors produce a continuous current signal or voltage signal that measures the distance of the target object from the sensing device.
They also feature an almost linear output voltage. When choosing an analog output sensor, your choice generally comes down to analog voltage (0 to 10 V), or analog current (4 to 20 mA). To learn more about Analog Inductive Proximity Sensor [Working Principle, Features, Applications] please refer to our article.
High Protection Proximity Sensor
High protection class inductive sensors are sensors that are resistant in all conditions and works in harsh environments and are currently in use in virtually all industries.
Maritime inductive sensors and wash-down inductive sensors can be used in the manufacturing of this sensor. Maritime sensors are impervious and also corrosion-proof and resistant in saltwater.
wash down sensors are designed especially for the most demanding cleaning processes required in food and beverage applications.
Full Metal Proximity Sensor
Full-metal stainless steel housing is highly impact-resistant, resistant to chemicals, corrosion, and deformation, and also waterproof during high-pressure cleaning.
They are ideal for use in following industries food and pharmaceutical, beverage manufacturing, metalworking, and chemical. To learn more about Inductive Full metal Proximity Sensor [Structure, Features, Applications] please refer to our article.
Weld Immune Proximity Sensor
Weld immune sensors are used in welding areas that are capable of withstanding high-intensity magnetic fields as well as welding sparks and slags.
Magnetic field immune electronics, weld sparkle and weld slag resistance body, high-temperature resistance sensing face are some of the features of this product. To learn more about please refer to Weld Immune Proximity Sensors [Structure, Challenges and Solution, Applications] article.
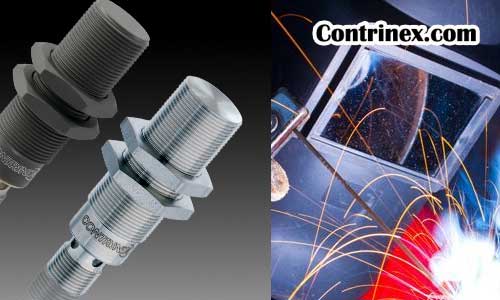
Inductive Proximity Sensor Working Principle
Inductive sensors detect metallic objects which are present in their determined space. In these non-contact proximity sensors, the operating principle is based on the interaction between the metal object as an electrical conductor and the emitted magnetic alternating field of the sensor.
Energy is extracted from the field by inducing eddy current, so the level of the oscillation amplitude is affected by this energy.
They consist of four major components:
The coils that are located on a ferrite core and allow the magnetic field to escape in a specific direction.
An oscillator that generates a high-frequency magnetic field in front of the sensor, that radiates from the ferrite core, and a coil at the sensing face.
When a target enters this magnetic field, eddy currents are induced on the metal’s surface and extract energy from the oscillator.
So, the level of the signal in the oscillator changes. The change in signal level then switches the output amplifier in binary sensors via a Schmitt trigger.
In measuring sensors, this change in signal level affects the analog output signal depending on the object distance.
Inductive Sensor Wiring
The most popular types of proximity sensors is the 3-wire type. They use PNP or NPN type transistors to switch the output when an object is detected. Depending on the types of output the way that load is connected to the sensor can be determined. It’s worth mentioning that if they are physically similar but interchangeable usage of them can lead to damage.
every switch has 2 functions: Normally Open (NO) or Normally Closed (NC) contacts. During damping with an object, sensors with normally open functions establish contact connections, while sensors with normally closed functions disconnect connections.
In a 3-wire configuration, two of the three leads supply power while the third switches the load. The term load identifies as the sensor powers. The load could be a lamp, pneumatic valve, relay or machine alarm, PLC input (programmable logic controller) DC input that is the most common type. A typical 3-wire DC sensor’s output has a rating of 100mA to 200mA.
When a target object approaches the sensing field and is detected by the sensor, an induction current (eddy current) flows in the target due to electromagnetic induction the sensor output turns on. Standard color coding for 3 wire Proximity switches is.
Brown=Positive (+), Black=Load, Blue=Negative (–)
But 2-wire sensors can pilot a load connected in series. in this type of sensor, separate connections for the load circuit and the voltage supply can not be found. as an active component, 2-wire sensors require energy to function. the demanding electrical energy for the sensor supplied by two connecting wires.
At the same time, the sensor signals its switch state via the same two connecting wires. Theoretically, the sensor is easily replaced by a mechanical switch that is open or closed depending on the sensor damping situation.
Inductive Sensor vs. Capacitive Sensor
The proximity sensor provides information about the closeness of the sensor to nearby objects. There is no physical contact between the object and the sensor.
This non-contact feature causes the long operating life of the sensor compared to those sensors that detect objects by physically contacting them. Therefore detecting an object without touching it, does not cause abrasion or damage to the object.
Type of proximity sensor determined based on the nature of the object to be detected. For example, plastic objects can be detected by a capacitive proximity sensor and an inductive proximity sensor always requires an object made of ferrous metal.
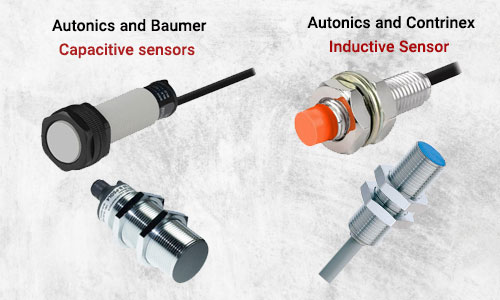
What is a capacitive sensor?
Capacitive switches are a non-contact electronic device that senses metal as well as nonmetallic materials. Some examples of the materials a capacitive sensor can detect are all types of metal, all types of plastic, wood, paper, glass, and cloth.
Detecting liquids or products can be used for the presence detection of grain in a feed silo, for example as a level measurement or full and empty detections. The shape and color of the target object do not affect the operation of the sensor.
How does a capacitive sensor work?
They are similar to inductive sensors. The capacitive sensor works by measuring changes in the capacitive field. the sensor emits an electrical field from the sensing end of the sensor to detect an object.
When an object comes near the sensing surface, it enters the electrostatic field of the electrodes, and the capacitive field changes. The air is in many cases constant.
The object that passes the sensor has a higher density than air, so the sensor switches.
Mounting of inductive and capacitive sensors
Flush and non-flush are the 2 methods of mounting for inductive and capacitive sensors. When choosing a mounting method, the sensor model should be closely considered.
However, oftentimes the most important is the effect the mounting technique will have on the detection range and the moment when an object is detected.
In a flush mounting, the sensor is flush with the mounting surface. Non-flush sensors, on the other hand, require some free space around the sensing face and protrude a little from the surface. a flush (shielded) sensor has a sensing field that will only sense objects that approach it from the face of the sensor so it has the shortest sensing range.
But Non-flush sensors (Unshielded) offer the longest sensing distance range because the sensing field extends from the sides of the sensor face as opposed to the edges or strictly the front of the face.
Inductive Proximity Sensor Terminology
Sensing distance
The sensing distance is the distance between an object and the sensor surface at which a sensing signal is generated.
Standard target
A standard target is square, 1mm thick, and made from type FE360 carbon steel. The length of the side of the square is equal to the diameter of the sensor’s active surface, or three times the rated operating distance (Sn), whichever is greater.
Nominal sensing distance Sn
The nominal sensing distance Sn is a device parameter that does not take into account sample variances and external influences such as temperature and supply voltages.
Effective sensing distance Sr
The effective sensing distance is the operating distance at nominal voltage and a nominal temperature of 23°C. It is between 90 % and 110 % of the nominal sensing distance.
Usable sensing distance Su
The usable operating distance is the entire acceptable temperature and voltage range between 90 % and 110 % of the effective sensing distance.
Assured sensing distance Sa
The assured sensing distance takes into account all the external influences and sample variances and must be in the range from 0 % to 80 % of the usable sensing distance. Within this range, a guaranteed switching is ensured.
Reduction factor
when an object comes within the sensing area of the sensor, the impedance in the coil starts to change and the sensor can detect the metal object. the sensing distance of the inductive proximity sensor for different metals is different. The type of the target material has a big effect on the sensing distance of inductive proximity sensors. So, if the nominal sensing distance multiplies by the reduction factor the actual sensing distance for the target material can be determined and the performance of the sensor is found.
Factor 1
standards inductive sensors vary from one metal to another and when the sensing distance is reduced, they can detect only metal objects. To overcome this drawback, reduction factor 1 sensors solve this issue by using of a microcontroller. So factor 1 make sensing distance for all type of metals. So it provides for its users more flexibility, additional features, and diagnostic options. Inductive sensors with reduction factor 1 can also be used as a temperature indicator if needed and since in high sensing speed, they operate well used to detection of aluminum and nonferrous metals.
Hysteresis
The switching hysteresis is the distance between the turn-on point while approaching an object and the turn-off point during the separation of it from the sensor. The hysteresis brings about a stable switching signal even when there are vibrations, temperature drift, or electrical variations.
Switching frequency
The switching frequency of the sensor is determined as the highest possible number of switching per second according to standard measurement plates to EN 60947-5-2.
Resolution
if the smallest change in the distance from the sensor to the target object is made, this change is represented by the sensor into a measurable change in signal. high-frequency electrical noise and digital/analog converters can affect the operation of the resolution.
Dynamic resolution
At fast measurements or scanning at high rates, dynamic resolution is required. Due to this, measurement noise produced can not be filtered or limited filtration can be done.
Static resolution
Opposed to dynamic resolution, the static resolution is used when there is slow movement or scanning at low rates. So the filtration of measurement noise is possible and this filtration does not affect carrier signal. This method causes the resolution to be increased.
Repeat accuracy
repeat accuracy can be defined as variations in sensing distance between successive sensor operations under determined conditions of 8 hours and temperature of +23 °C ± 5 °C.
Response time
when the target object moves into the sensing field, a time interval is needed for the sensor to be activated and the output turns. The output signal reaches 90 % of the maximum signal level at this time.
FS Linearity
Full scale or FS Linearity is when the output signal deviates from the ideal straight line and an error occurs. Also, it is the percentage of the measurement range. In situations where there is a lack of linearity, sensors with linearized output, and the Polynomials linearization technique can be replaced.
Output
DC Voltage
2 wire DC: This type of system is used for the transition of DC power. there are 2 connecting wires. The load is connected in series with the sensor in the circuit. The required current of the sensor is connected to it through a resistor or load. As a result, when the sensor is off (open), a weak current passes through the resistor (to power the sensor itself) and when the sensor is connected (closed), voltage is generated on the sensor. There must be current and voltage at all times in this type of sensor. So there will never be clear cases of open and closed. Inductive sensor output is as normally open NO and normally close NC.
3 & 4 wire DC: there is an output amplifier in this type of sensor. 3 wire type supplied with function N.O. or NC while 4 wire type complementary outputs (NO + NC) in the types NPN and PNP. in standard version protection against short circuit, polarity, and peak ensured that this protection is through the disconnection of inductive loads.
Analog & Linear: current or voltage output in the 3 wire sensors is based on the distance between sensors and detected metallic object.
NAMUR: This type of sensor is a two-wire sensor whose internal resistance varies according to the distance of the object from the sensor and often works with a separate switching amplifier. They are reacting against metals, this reaction appears as voltage or linear current at the output. These sensors are used in hazardous environments where there is a risk of explosion and ignition due to the limitation in their current and voltage.
AC Voltage
2 wire AC: 2-wire AC are the sensors that operate in series with the load and are connected to alternating-current supply voltages and contain a thermistor output amplifier. When the sensor is in open function, a residual current moves in the load, and in closed function, dropping of voltage occurred in the sensor. this type of sensor does not have transistor output, so they have a much lower operating frequency than dc sensors. Ac inductive sensors are relatively more resistant to electrical noise than DC sensors. The electromagnetic waves formed around the AC sensors are more resistant to intense noise than the DC sensors due to the input power supply. Therefore, they have a more stable performance in noisy environments.
Definitions of Output
NO (normally open): If the sensor is in the normally open configuration When the target object enters the Sensing area, its output will be converted to an ON signal.
NC (normally closed): If the sensor in the configuration is normally closed, when the target object enters, the sensor generates an OFF signal at the output, and has a voltage at the output
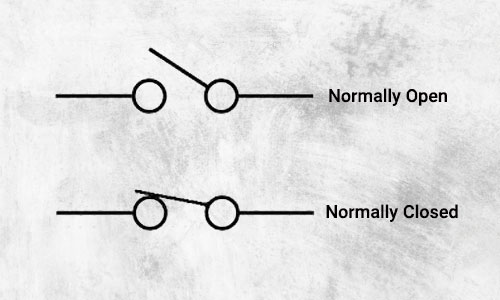
NPN Output: An NPN output is known as a sinking output. When the sensor senses an object and the power supply is established, voltage is applied from the negative power supply to the output. In this type of sensor two wires are used for the power supply and one wire is for sensor output.
PNP Output: A PNP output is commonly known as a sourcing output. As the power supply is established and the object is placed in front of the sensor, voltage is applied from the positive power supply to the output. In this type of sensor, two wires are used for the power supply and one wire for sensor output.
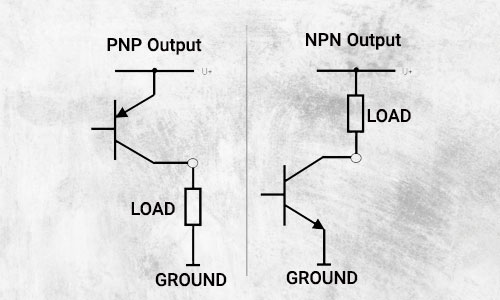
Power Supply: A power supply is a device that supplies power to an electric load. It provides a voltage that sensors are required to operate.
Max Switching Current: It's the maximum current that can flow through the sensor and it can be sensed by the contacts.
Min Switching Current: A minimum current indicates the smallest current that can flow through the sensor.
Max Peak Current: It is the maximum amount of current which the device is capable of operating for brief periods without suffering either performance degradation and will not cause any damage to the sensor.
Residual Current: It is an electric current that continues to flow in a sensor when there is no voltage.
Power Drain: It refers to the use of power and the amount of it that the sensor requires to operate.
Voltage Drop: The voltage drop occurs when the amount of voltage decreases through all or part of a circuit due to impedance.
Short Circuit Protection: It is defined as the excessive flowing of current beyond the current rating that damages the sensor.
Operating Frequency: This is the maximum number of times the waves repeat or complete a cycle within a one-second time period.
Repeatability (%Sn): the repeatability of the sensors was evaluated by the differences of sensor outputs when approaching the same point at 8 hour period and temperature of 15 to 30ºC and a supply voltage with a <= 5% deviation.
Flush Mounting: In flush mounting, the surface of the sensor is flushed with the damping material affixed around the sensing face to protect the face of the sensor
Protection Degree: It is enclosures that provided for electrical equipment to protect them against solid foreign objects, against water, and against access to hazardous parts.
Advantages of Inductive Proximity Sensors
• Detection without any touching
• Reliable function in harsh environment
• Long service life because there is no moving part
• Simple structure and cheap in price
• High measurement accuracy
• High sensing rate
Disadvantages of Inductive Proximity Sensors
• Limited detection range
• Sense only metallic objects
• High temperatures, cutting fluids, or chemicals can affect the operation of the sensor
Applications of Inductive Proximity Sensors
The design, flexibility, and exceptional performance of inductive sensors make them an ideal fit for a wide range of various applications and industries
• Used in industrial machinery
• Motion position detection and motion control and mechanical motion detection
• Production of coils and transformers
• In traffic lights and traffic control and metal detectors
• Automatic car washes
• Detection of elevator door closure
• In the industrial sector, the inductive sensor is used in counting parts systems, separation of parts with different dimensions