Detecting Bottle Caps through Cardboard Case on High-Velocity Packaging Lines
In beverage manufacturing, a final, pre-shipment check is done on all bottles after the corrugated cardboard case has been sealed. Bottles can be located in a wrong way or may be absent or their caps can be missing.
Hence, the challenge is to figure out caps via several layers of corrugated cardboard material of various density and thickness.
Basic variety of inductive sensors, with working distances 3x the usual sensing variety, are suitable for this application. For every lane of bottles in a case, one 30 mm diameter inductive sensor is established. The 30 mm non-embeddable sensor is selected because it most closely equates to the scale of the bottle cap and yields the best detection distance for the available target area.
The prolonged detecting distance is enough to allow for minor variations in the height of the case as it passes under the sensor bridge. This warrants reliable sensing and keeps the sensor at a secure distance from any impact, keeping off consequent downtime. Some warning must be considered in mounting and spacing of the sensors so as to minimize the probability of cross talk (mutual interference).
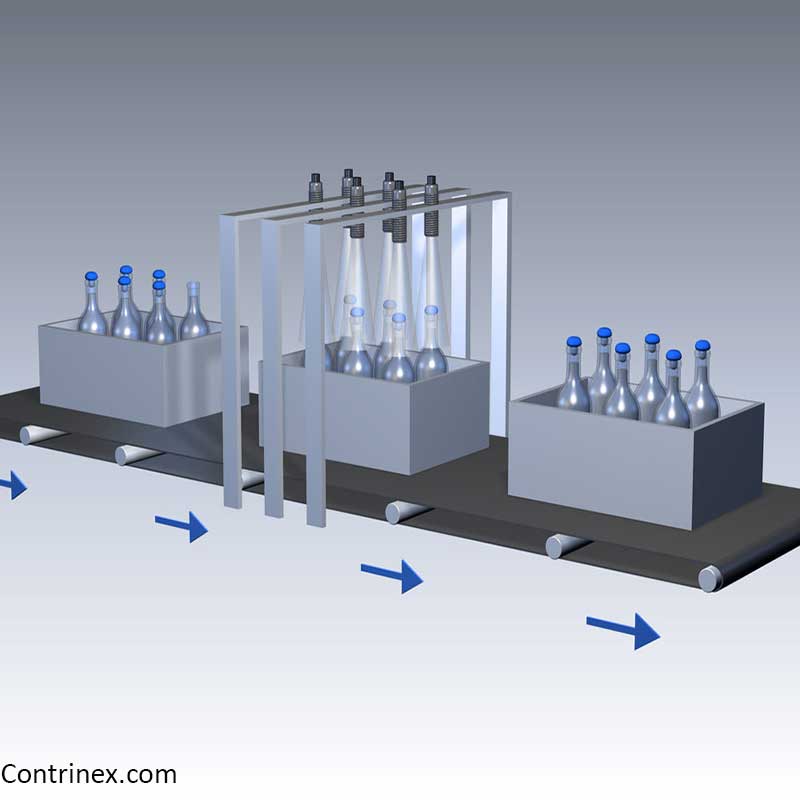
Do You Need Help For Field Installation?
We have thought everything through, submit your request for an on-site support.
Do You Need More Solutions? Have a Look at Our Vast Applications
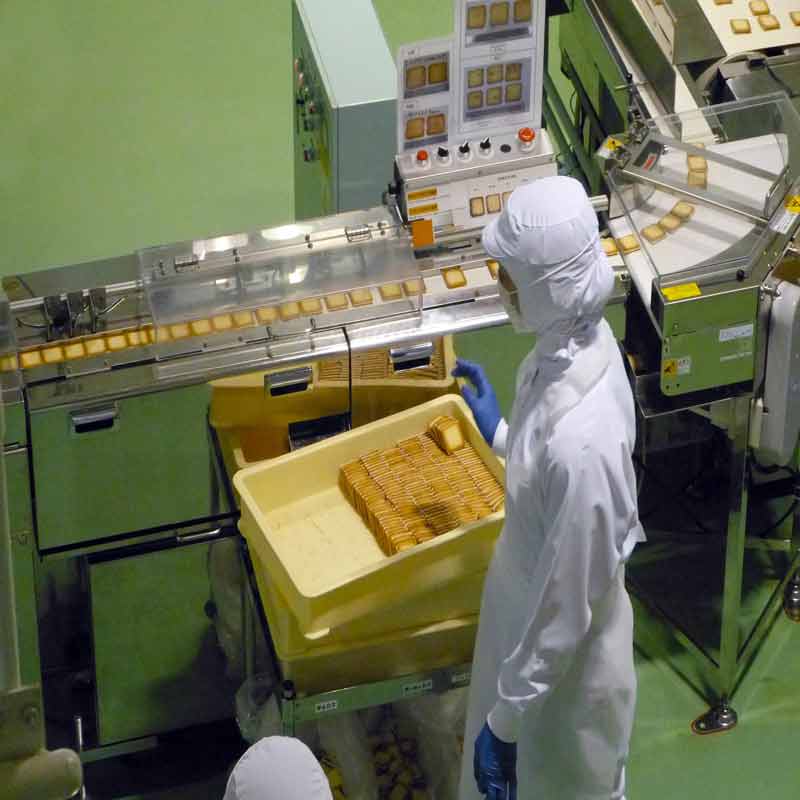
Reliable Tool Changing in Packaging Machines by RFID
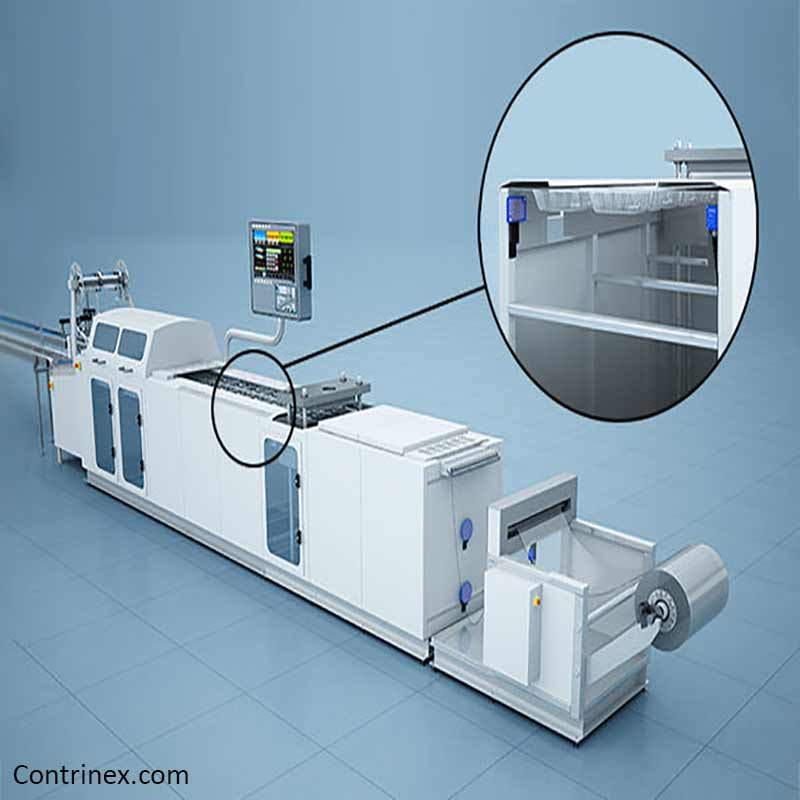
Transparent-Object Sensors with Patented UV Technology for Reliable Detecting and Precise Counting of Clear Plastic Trays
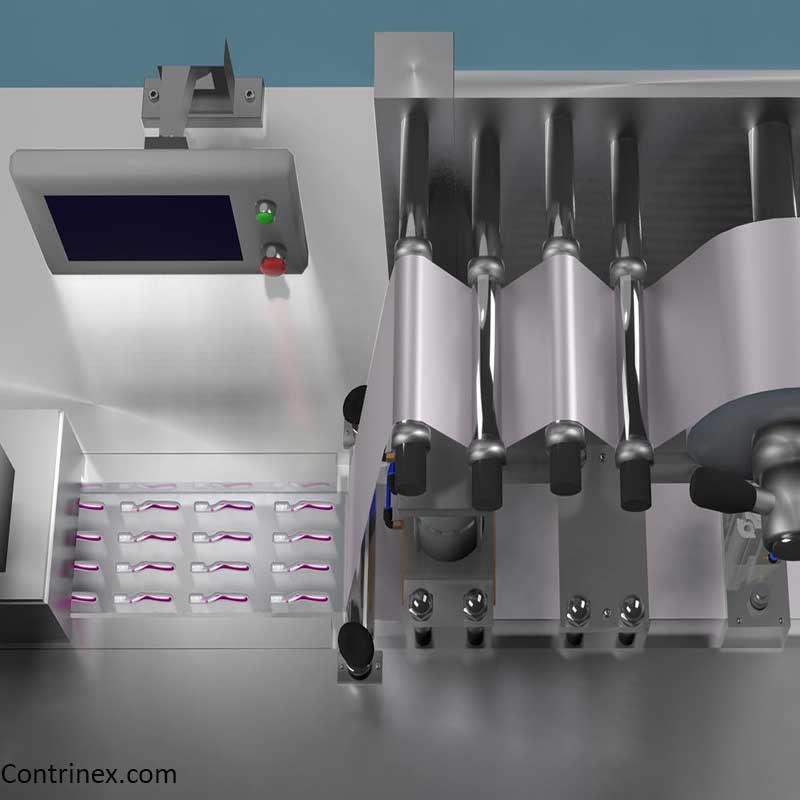
Figuring out Translucent Targets during Blister Packaging via Fiber-Optic Sensing with Blue Light Source
Related Products