Industries
After the industrial revolution and the boom in science in recent centuries, there is no know-it-all. Every part of our needs is handled by a specific industry. Our food, drinking, space curiosity, travelling, love for fashion and jewellery, breathing clean air, …, they all depend on their specific industry.
Here at our industry page you can find applications for each industry and for each application you can find the related products.
In case you're interested to know specifically about pressure sensor use, don't hesitate to click on the below button.
Choose Your Industry
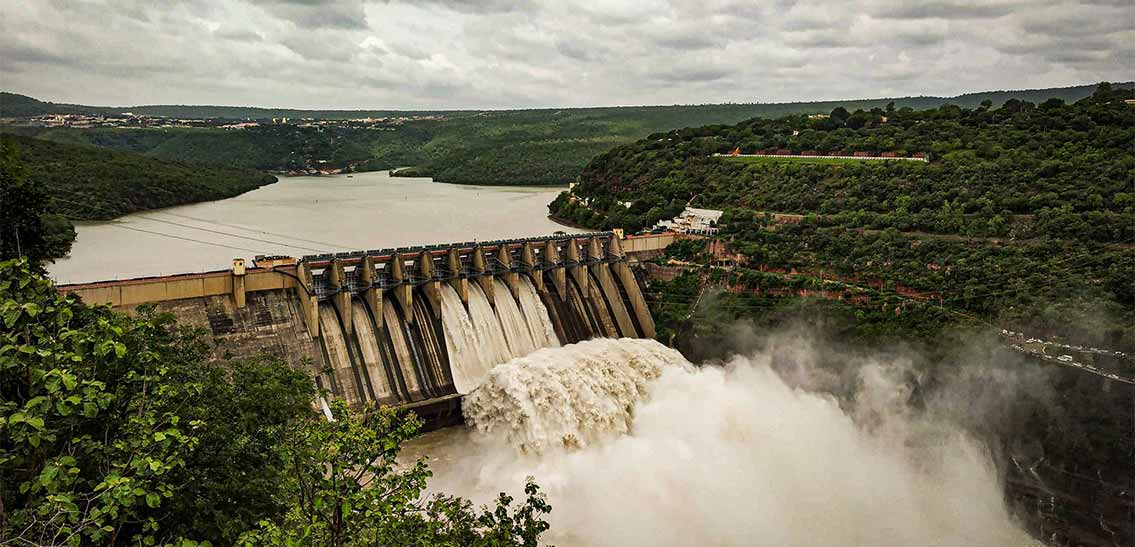
Water & Wastewater Treatment
The water and wastewater industry primarily includes water treatment, ETP (Effluent Treatment Plant), STP (Sewage Treatment Plant), and ...
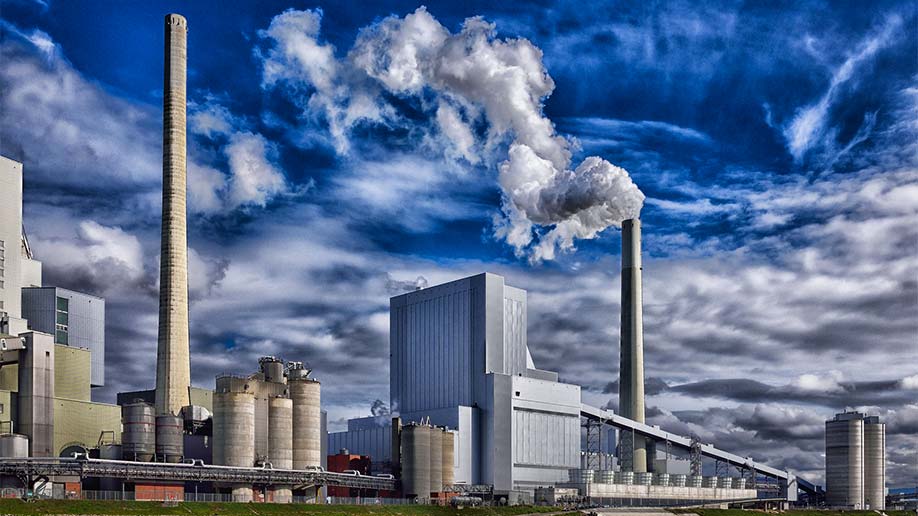
Chemical, Petrochemical and Refining
The Chemical, Petrochemical, and Refining industries are the foundation of the manufacturing processes and operate in a global ...
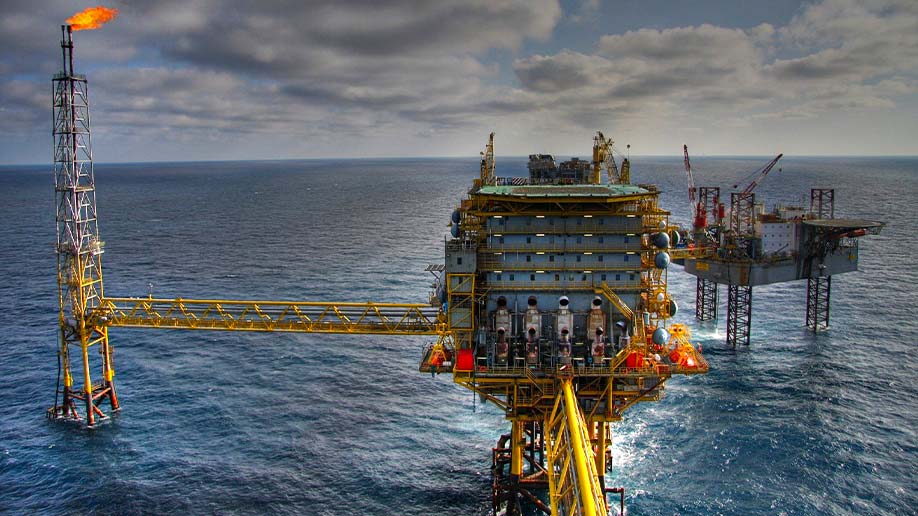
Oil & Gas
Oil and gas as the world's primary fuel sources are important and major industries in the energy market and play …
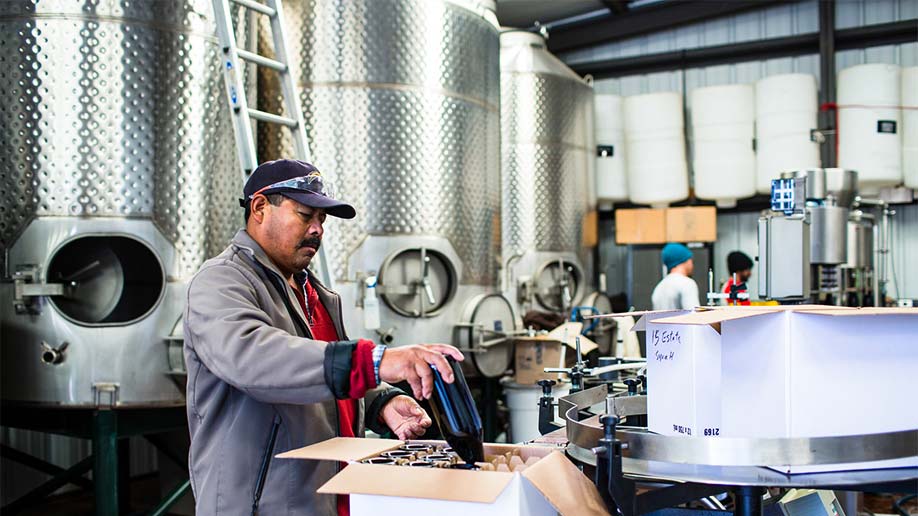
Food & Beverage
Food and beverage industry is one of the most rapidly growing manufacturing sectors and includes all aspects of the industry …
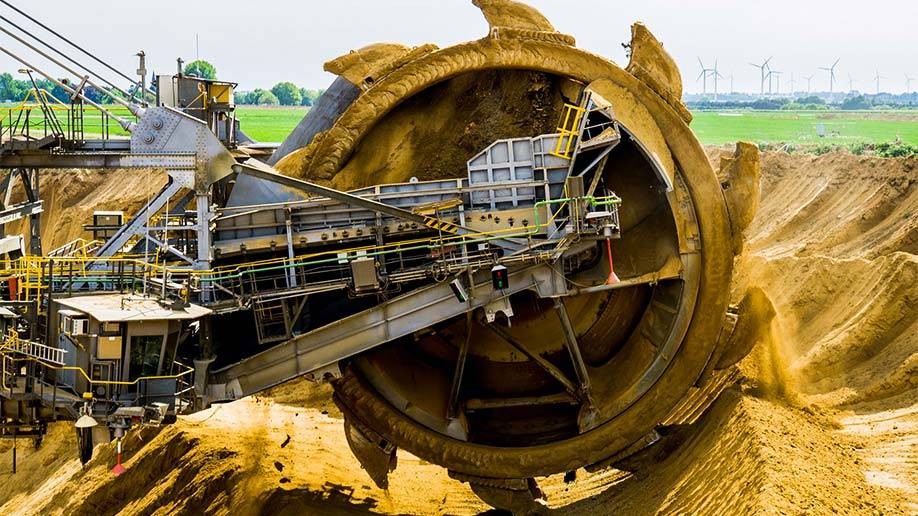
Mining, Minerals & Metals
The mining, Minerals & Metals industry is related to activities that include steelmaking, locating, excavating, and processing ...
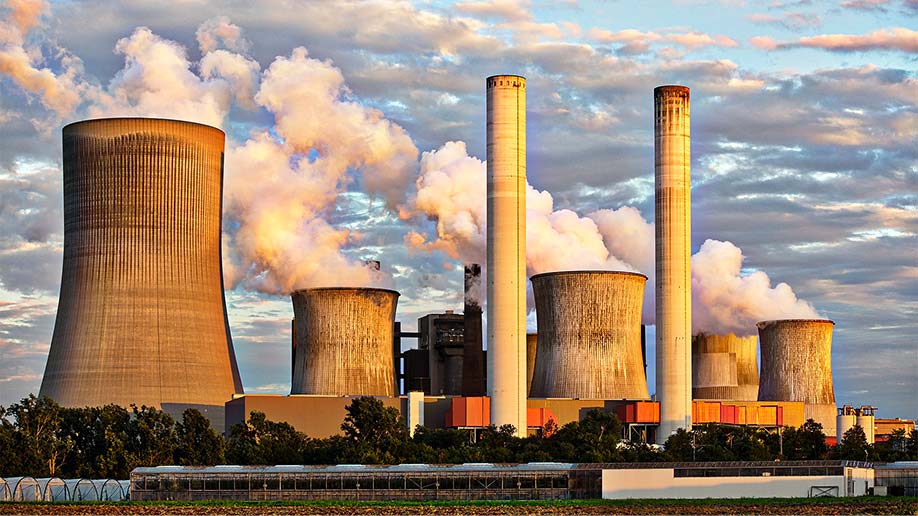
Power & Energy
The power & Energy industry is perhaps the most important sector for the constant production and distribution of energy required to …
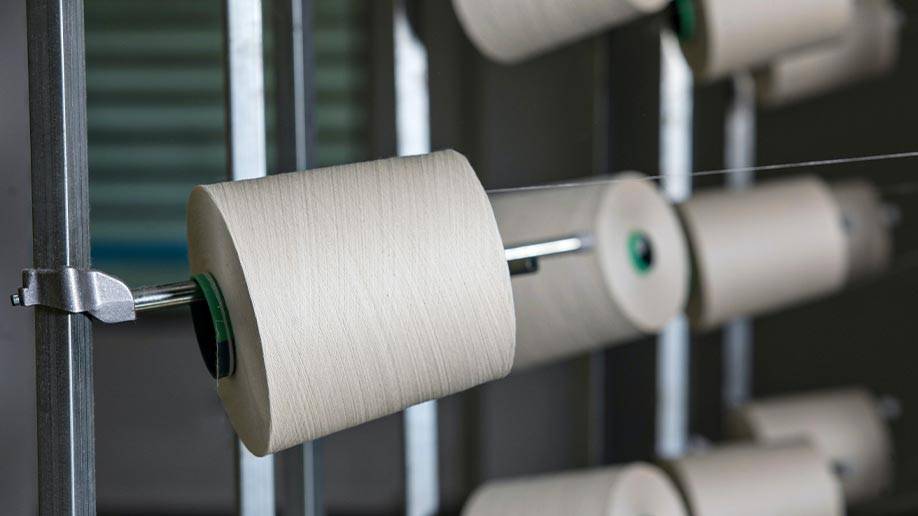
Textile
The textile industry is one of the largest markets in the entire world and is the foundation for a number of other industries.
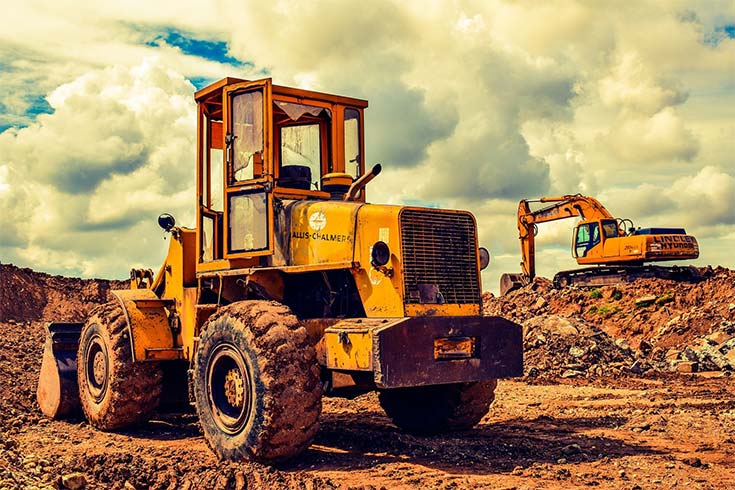
Mobile Equipment
The mobile equipment industry supplies equipment used in industries such as construction, material handling, mining, rail maintenance, …
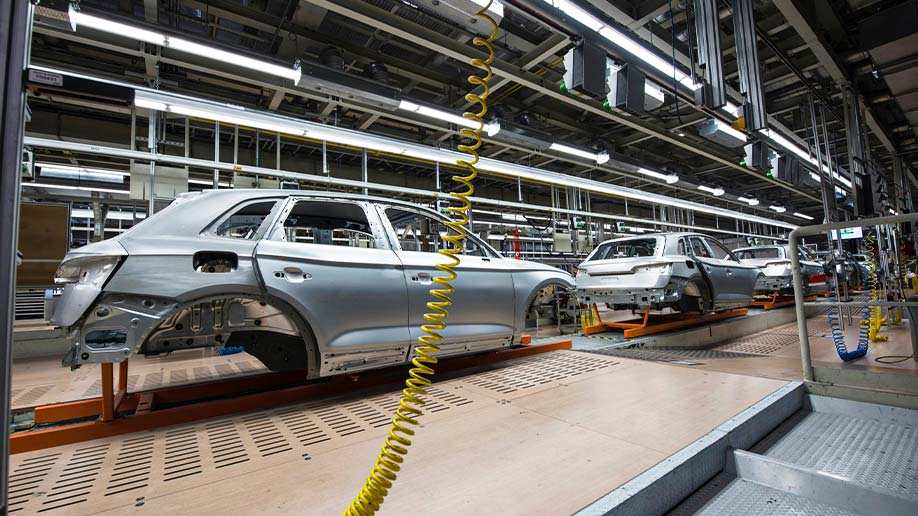
Automotive
The automotive industry is a vital part of the world's economy and includes a broad range of companies and activities involved in the engineering, designing, ...
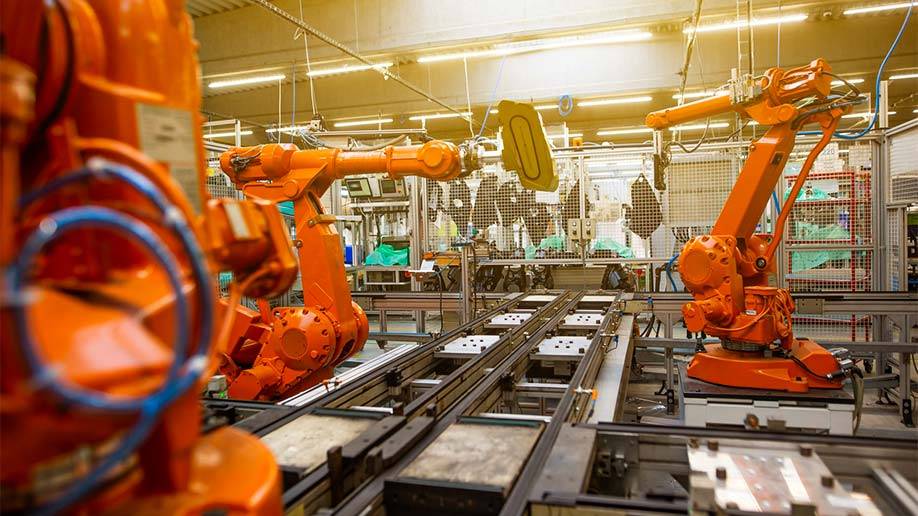
Factory Automation
The mechanical and automation industry is a broad discipline that is continuously evolving and mainly focuses on the branches of …
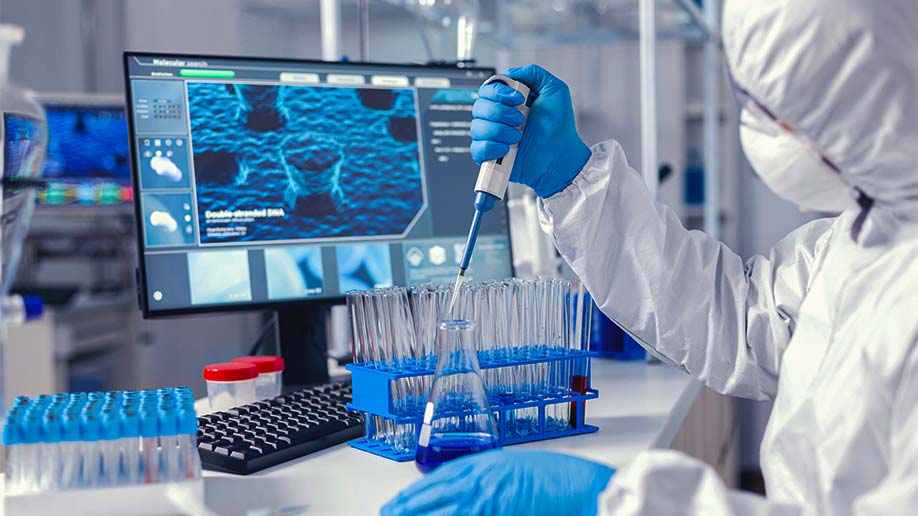
Medical & Pharmaceutical
The Medical & Pharmaceutical industry plays an active role in the discovery, development, and manufacture of drugs and ...
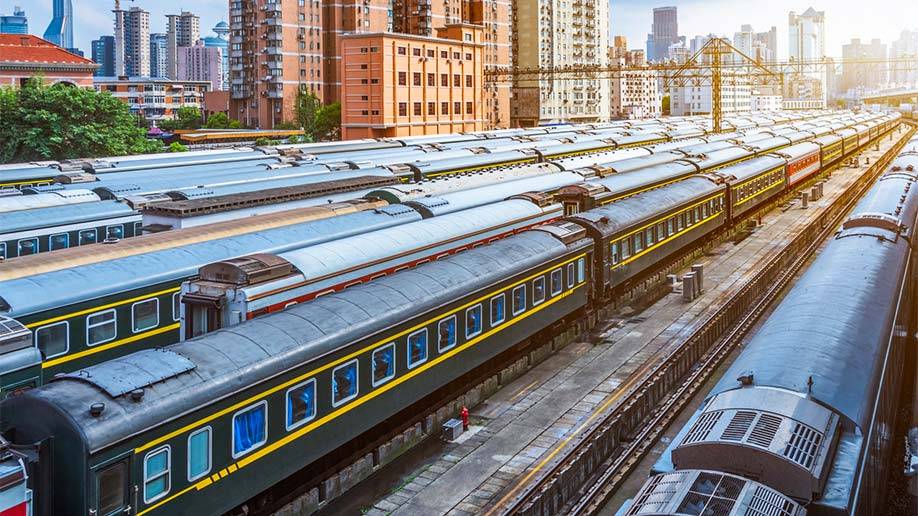
Railway Technology
The rail industry is an essential part of transportation infrastructure and consists of the sale, manufacture, and operation of railway technology.
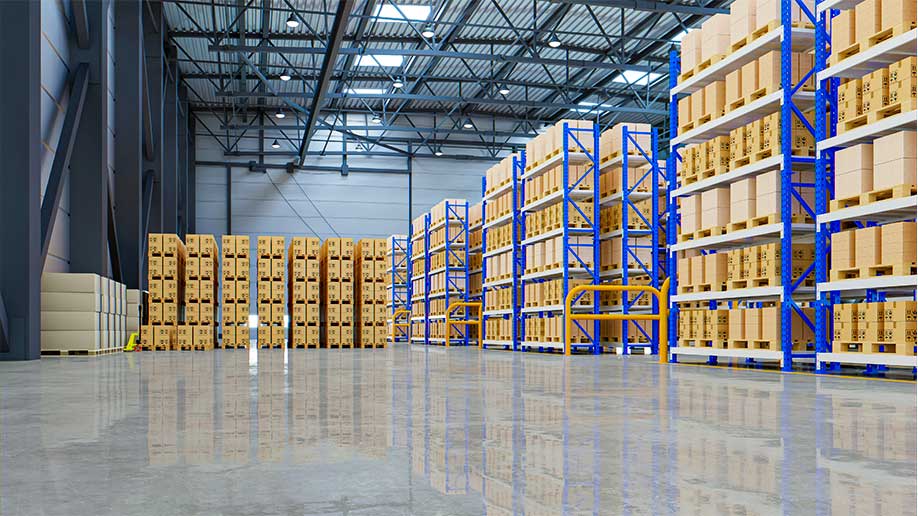
Packaging, Pulp and Paper
The pulp and paper are one of the largest and most complex industries in the world with many different kinds of products …
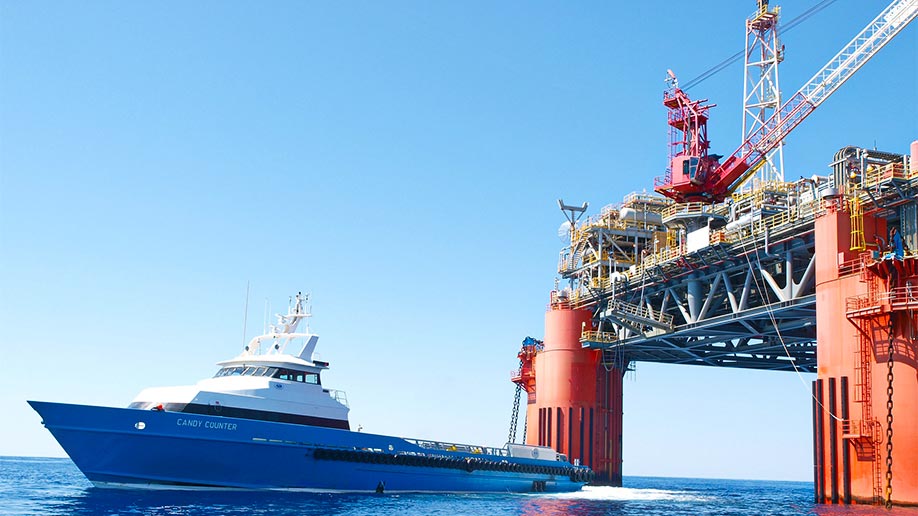
Marine and Shipbuilding
The shipbuilding industry is an important and strategic industry related to the production of larger sea-going vessels used for ...
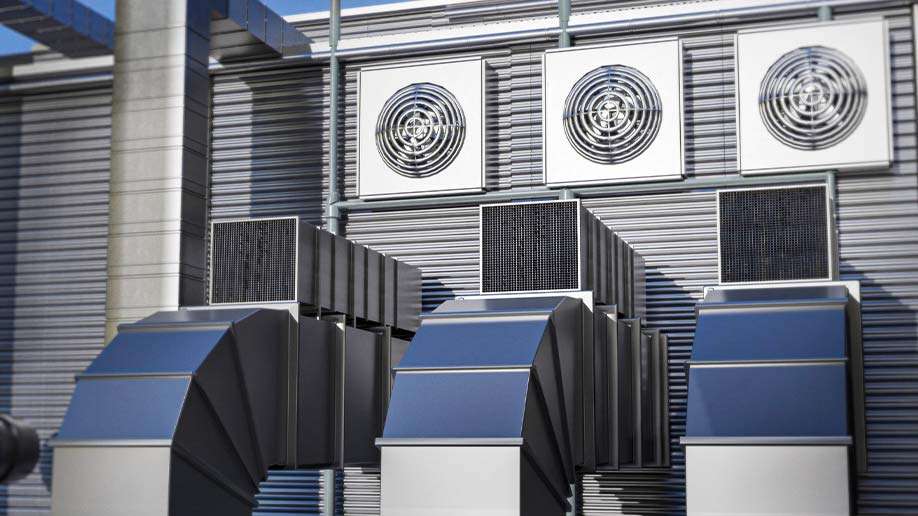
Heating, Ventilation, and Air Conditioning
The heating, ventilation, and air conditioning or HVAC industry is an important part of residential structures that contain portable air …
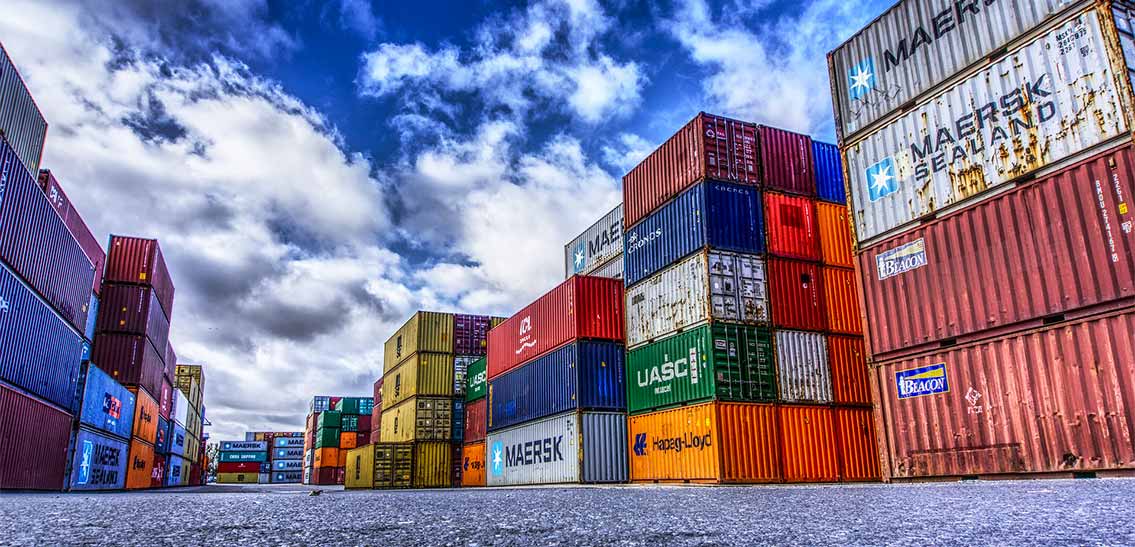
Logistics
The logistics industry, one of the backbones of international trade, is the science of obtaining, producing, and distributing material and …