Minimizing the Number of Double-Bottoms during Aerosol Can Manufacturing via Detecting Their Mass
A manufacturer of aerosol cans desires to make certain that, for every can, just one bottom is inserted into the press that applies and crimps the bottom to the can body. This checking has to be done without physical touch whilst the product is moving. But, the gage of steel used to supply the can bottoms (~ 0.33 mm in thickness) is too small for the sensing range of the client’s usual automatic double-sheet detector.
The special properties offer a simple, affordable solution. They work on the basis of Condet® technology, which allows them to figure out the mass of a target instead of simply its surface.
The sensor is established almost 4–5 mm above the intended target: the dome of a can bottom. On its own, the 0.33 mm thick target presents inadequate mass to switch the sensor at this distance. However the presence of a second bottom piece enhances target mass adequately to switch the sensor. This activates rejection of the double-bottom further downstream, in which the component is blown free.

Do You Need Help For Field Installation?
We have thought everything through, submit your request for an on-site support.
Do You Need More Solutions? Have a Look at Our Vast Applications
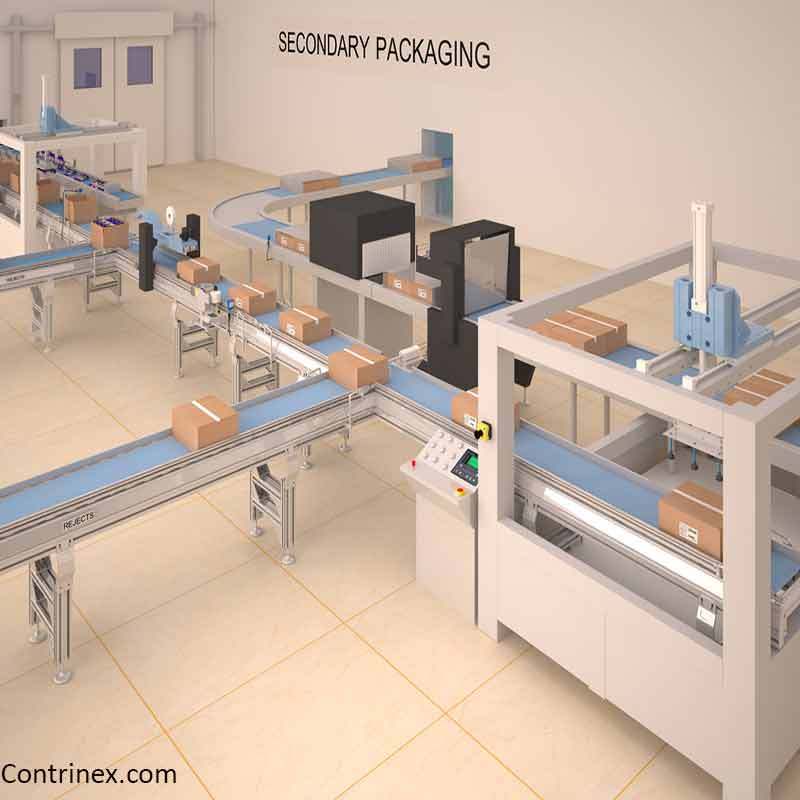
Using Photoelectric Sensors to Control the Process of Bulk Food Packing
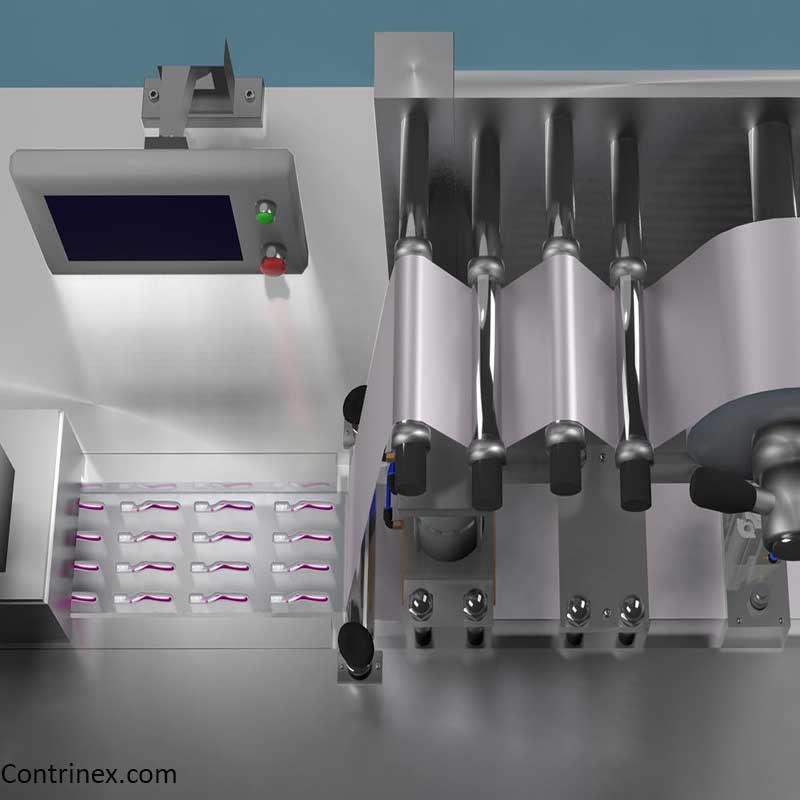
Figuring out Translucent Targets during Blister Packaging via Fiber-Optic Sensing with Blue Light Source
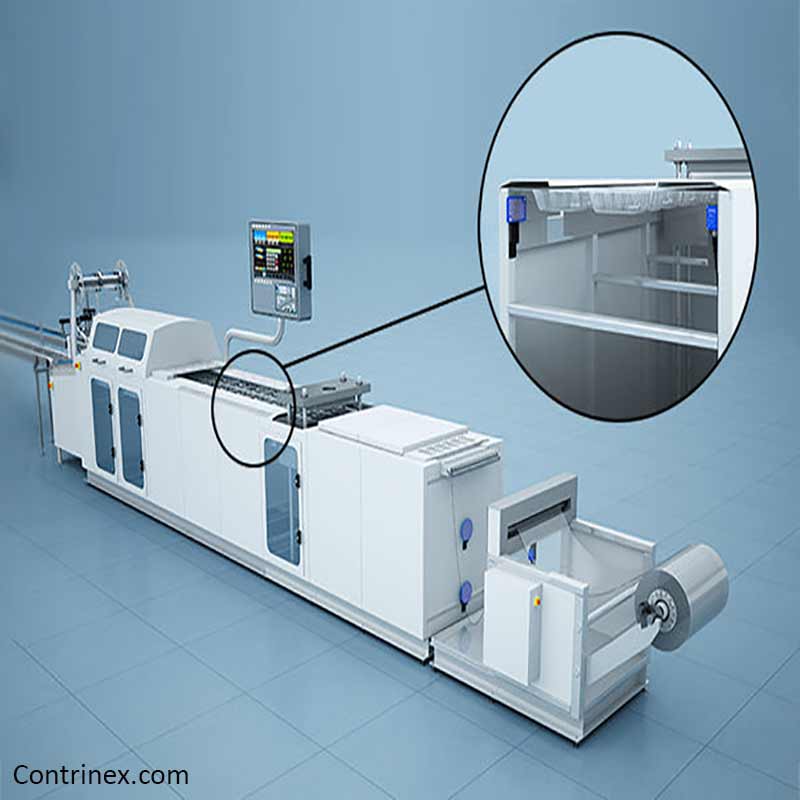
Figuring out Clear Plastic Sheets during Thermoforming through Transparent-Object Sensors with Patented UV Technology
Related Products